Project News
Hard Work Meets Great Preparation: The Runway 17R-35L Project Wraps Up
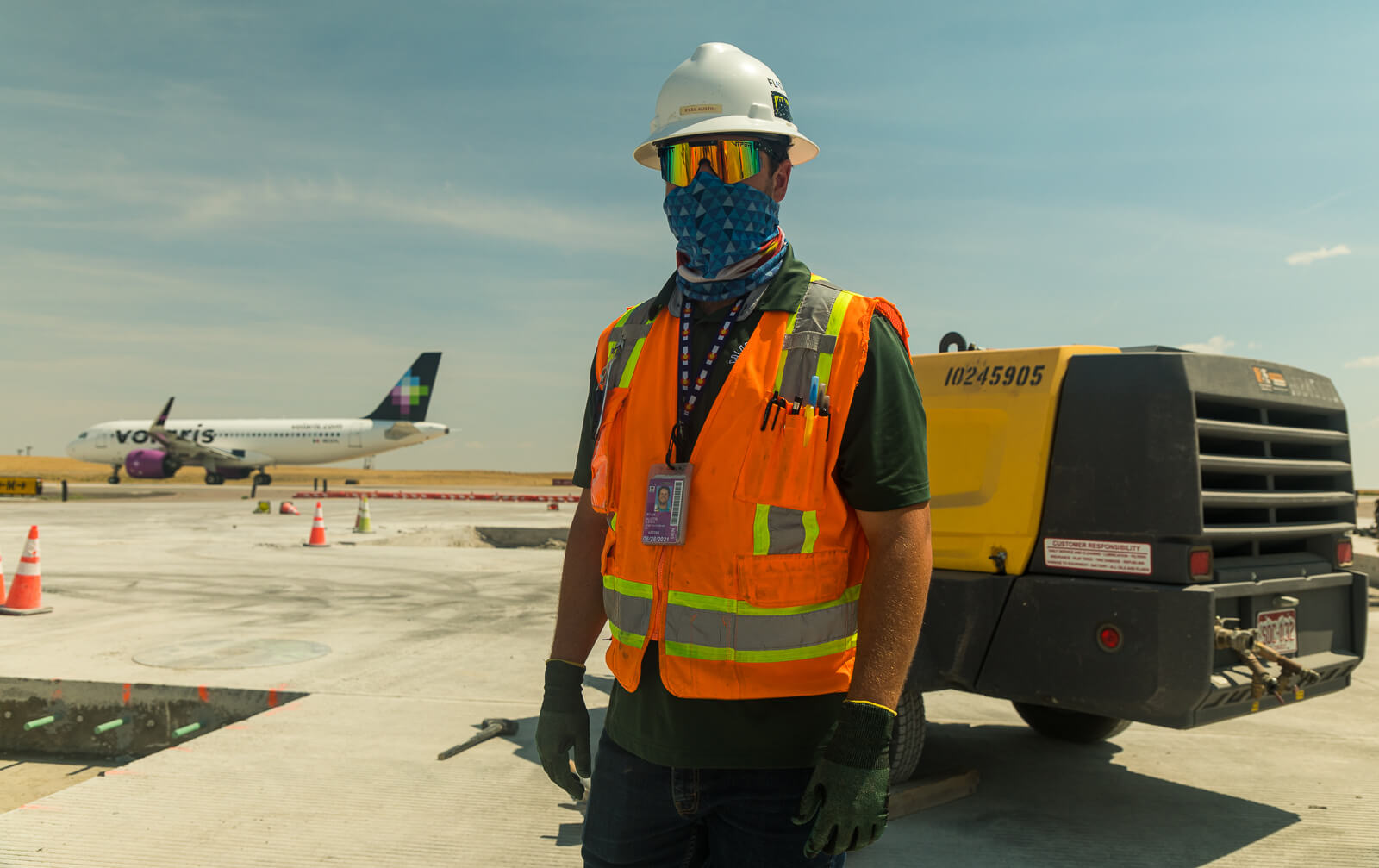
Justin DuMond was there at the beginning, at the end, and for all the fine details in-between.
The project manager put together the estimate for the $26 million hard bid Runway 17R-35L Rehabilitation Project for owner Denver International Airport. Flatiron was general contractor, working with a solid core of subcontractors.
DuMond worked through the holidays to have the bid submitted in early January 2020. However, being centrally involved early allowed DuMond to know who his “dream team” would be on the project. “We worked closely with selected subcontractors on our phasing and schedule during negotiations,” the project manager says. “We subcontracted with Royal Electric which had done some work at Denver International Airport years ago but was basically a new project venture for them. We had a great relationship with them with each side helping the other to succeed.”
Flatiron reached substantial completion at the end of September. Teams are now finishing up punchlist work. While the project has the name “runway” in the title, the actual work was on two adjoining taxiways: M and L. Flatiron removed and replaced more than 38,000 square yards of 17-inch deep concrete panels from those taxiways during the rehabilitation project.
The schedule was intensive: a duration of five months to hit substantial completion given the owner’s schedule. But Project Manager DuMond had the resources to do it, with a total of 100 Flatiron and subcontractor craft workers at the job’s peak.
He knew it would be hard work, but great preparation would be key as well. He started thinking ahead in the bid phase. “I went an extra week in planning in our look ahead plans. We wanted to make sure that our subcontractors were looking ahead to the next phase switch and the exact day that they would be needed on-site,” DuMond says. “As a result, there were only a couple of times when we had to rearrange subcontractor work activities because of scheduling availability.”
The hard work paid off. At its mid-summer peak, the project was producing $5 Million dollars in revenue each month. Flatiron and its subcontractors also completed each project milestone on time or early.
One shining example of that was the full replacement of High Speed Taxiway M6 between the runway itself and Taxiway M at the very beginning of the project. On the first workday Runway 17R-35L and a large portion of the taxiway were shut down for a span of 50 days (this was the first project milestone), ahead of having Runway 17R-35L and Taxiway M6 re-open on day 75.
Flatiron met the first milestone, and then had Taxiway M6 open on day 74.
Construction Manager Chad Danielson doesn’t mince words on how all this got done: “There were a lot of hours, a lot of dedication.”
Project Engineer Sushant Gupta says with the fast-moving schedule, no one could afford to take their eyes off the ball. “Even a one or two-day delay, could have led to a series of issues for us,” he explains. “Most of the work was sequential, the sealing team has to come in and start sealing the joints, so the paint company can come in and paint.”
Those long hours were also great opportunities for new field engineers like Martin “Marty” Heffren to develop new skills. He marveled at the project’s strong team dynamic and culture of mentorship. “There are so many people in Flatiron who you can rely on as resources, if you don’t know the right person you can call another project and someone will be happy to help.”
Danielson concurs that the collaborative spirit was top notch on the project. “I’m only as good as my team right?” he asks rhetorically.
This strong Flatiron effort didn’t escape the attention of the owner.
“Flatiron opened up the complex four days ahead of schedule, which is the earliest of any runway rehab in recent history,” said Denver International Airport Director of Infrastructure Mike Cloud.
CONTACT
Jason Evans
Marketing & Communications
JEvans@flatironcorp.com